Quality Control Process
Precision instruments to inspect the high-precision products
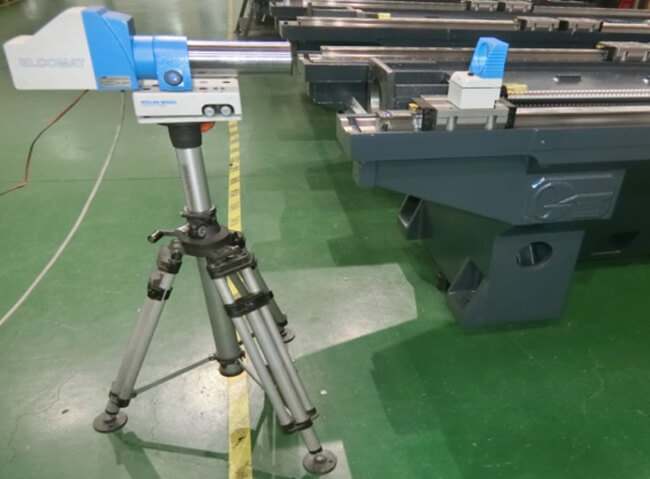
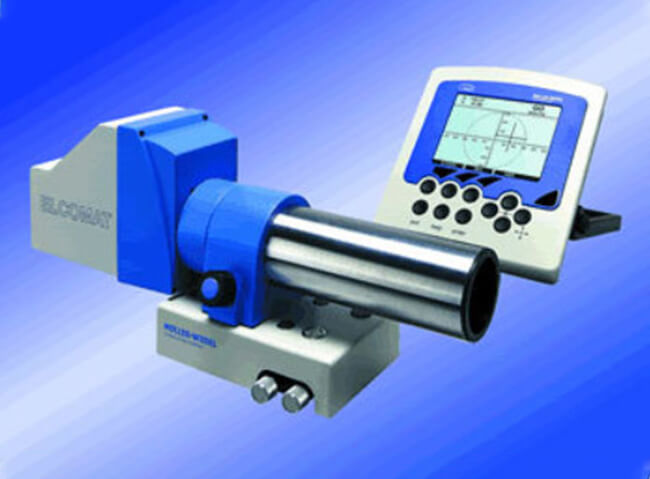
The straightness measurement of the large casting linear guide surface ensures that the parts quality meets the standards.
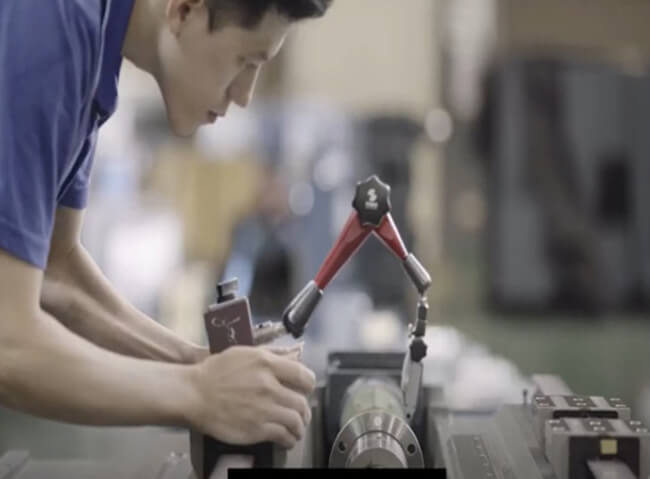
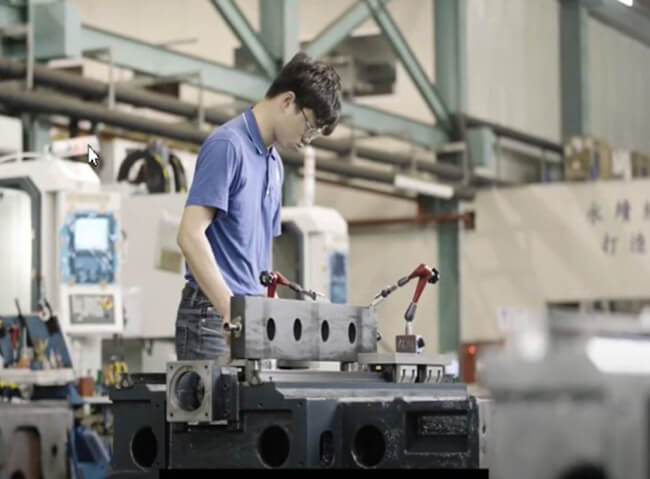
Independent inspection of the assembly accuracy to check the straightness of the linear guide, the parallelism of the reference plane and the side guide.
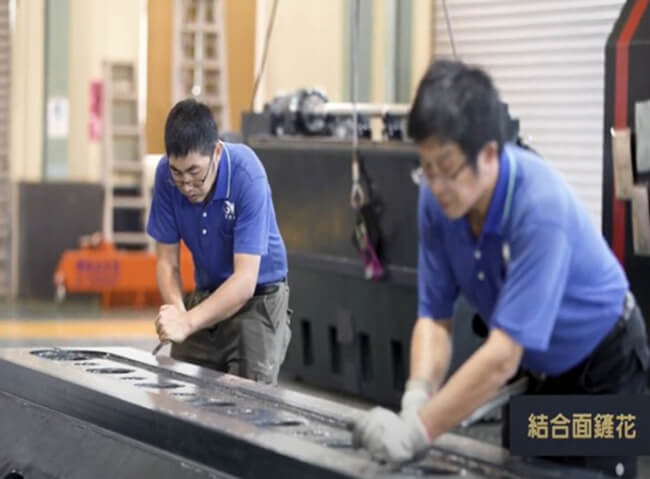
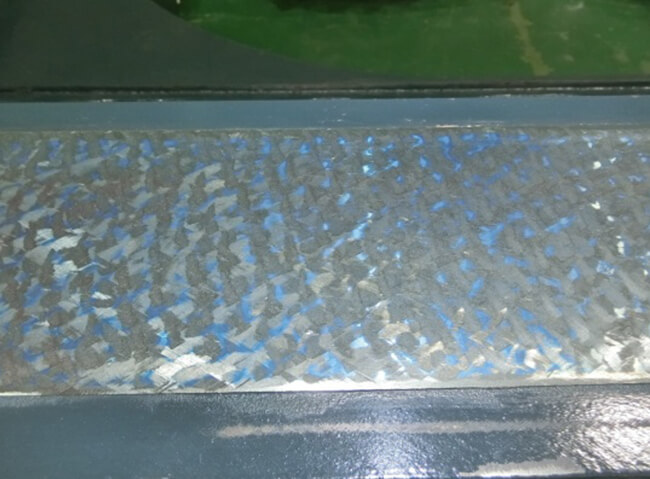
The GENTIGER strictly control the scraping of the surface. The important main parts are all printed and archived, and the scraping of the fixed surface that affects the accuracy is more important. The experience master makes the joint surface more flat by scraping.
Pursue the highest quality, and provide customers with high-reliability and high-precision products.

Check the right angle of the movement in each axis direction. (Angle square 300-500mm)
Specification:ISO 10791-2 (ISO 230-1)
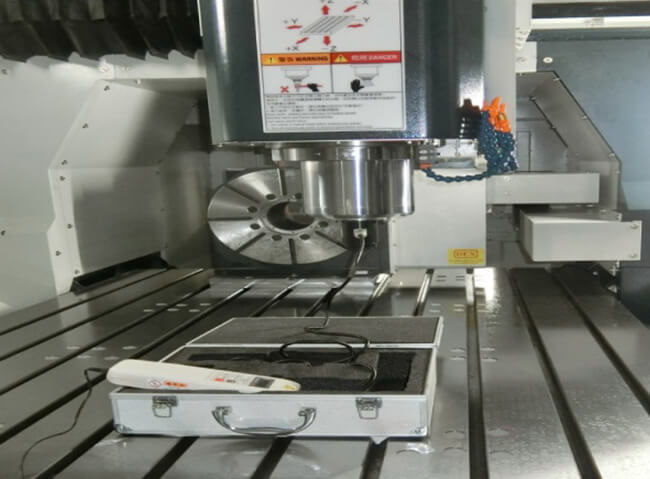
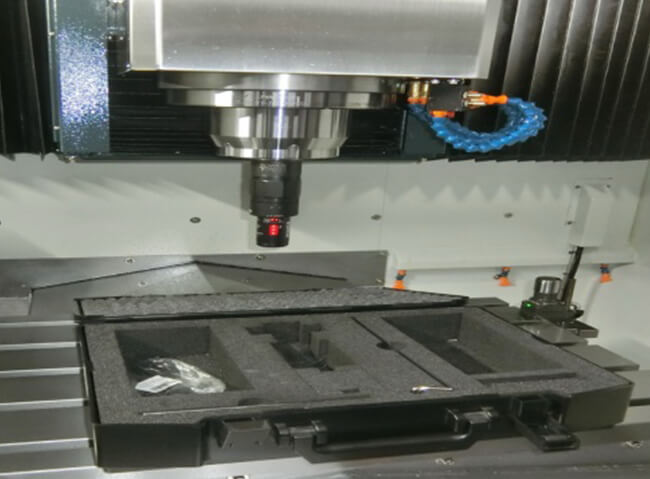
Check the value of the spindle clamping to ensure that meets the standard. (Tapper type:HSK and BT)
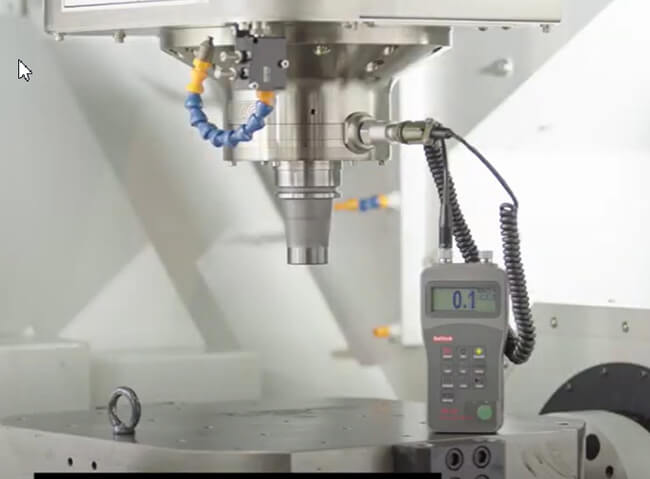
Check the spindle vibration value to ensure that the vibration meets the standard.
Specification:ISO 230-8
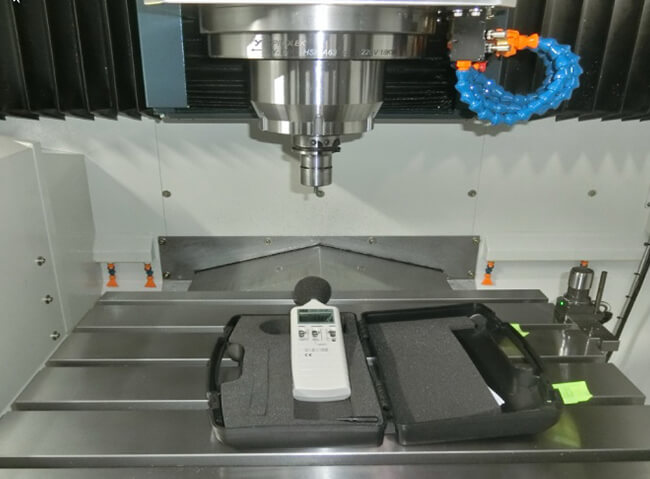
Check the spindle noise value to ensure it meet the standard.
Specification:ISO 230-5
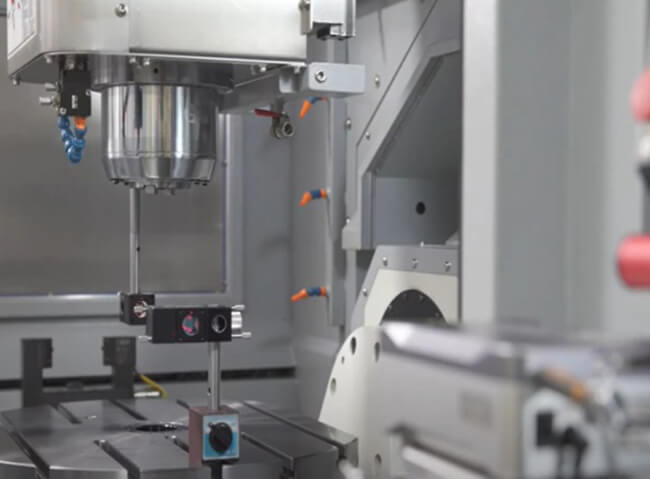
The accuracy of the all travel is compensated by the laser calibration and positioning accuracy to ensure the machine accuracy.
Specification:ISO 10791-4 (ISO 230-2)
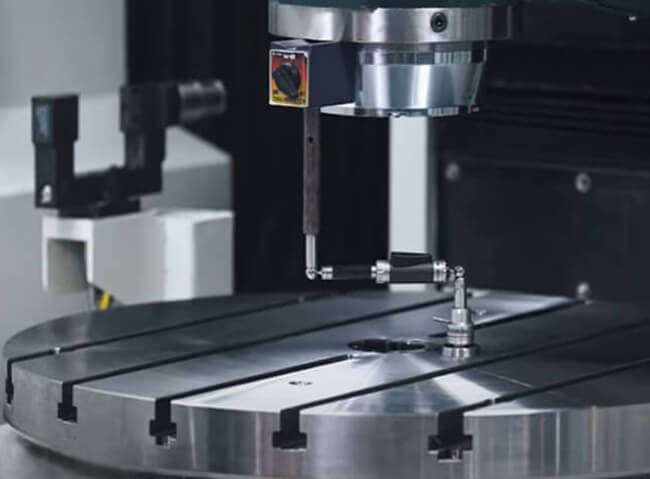
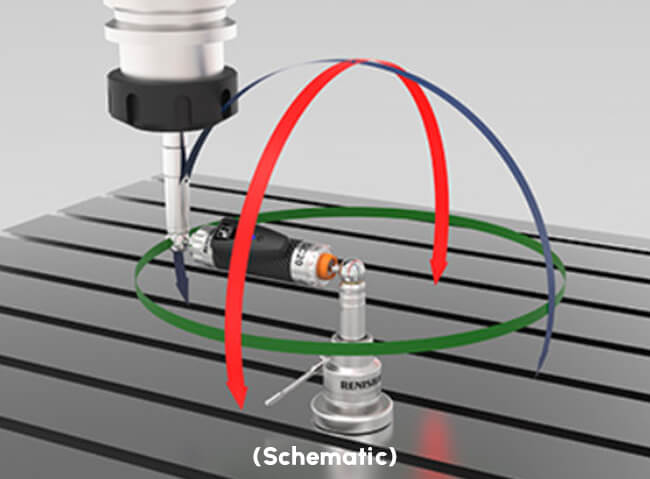
Correct roundness accuracy and machine geometric accuracy, to ensure the movement accuracy of the machine in three-dimensional space.
Specification:ISO 10791-6 (ISO 230-4)
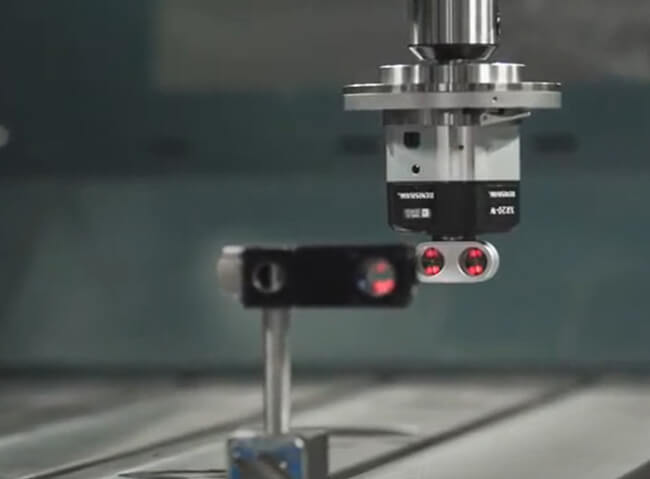
Rotary axis angle positioning accuracy, and repeatability accuracy inspection.
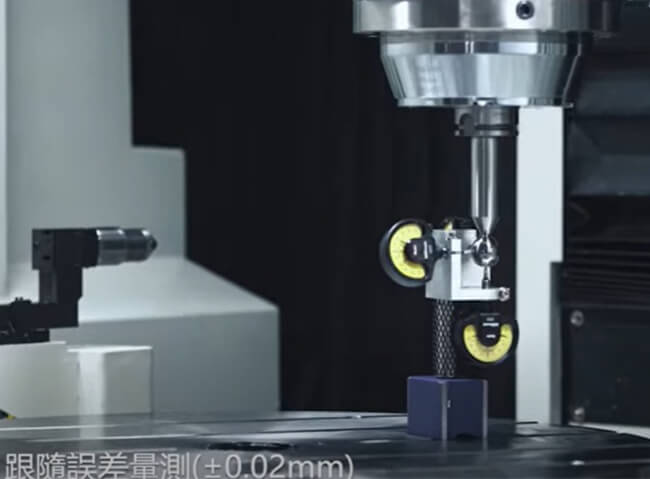
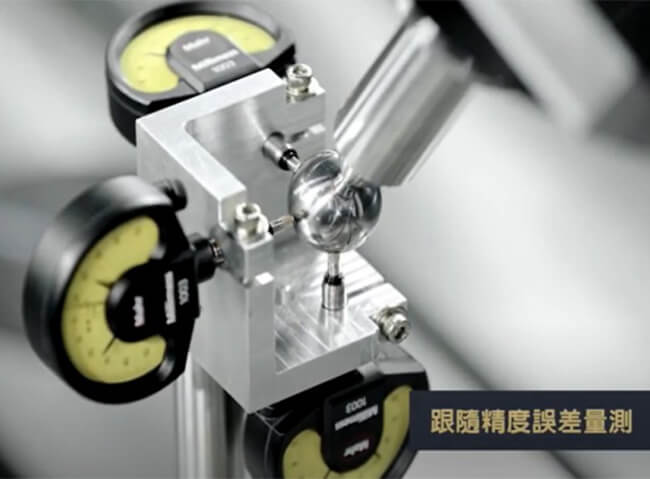
5-axis Dynamic Accuracy Inspection(Following error measurement)
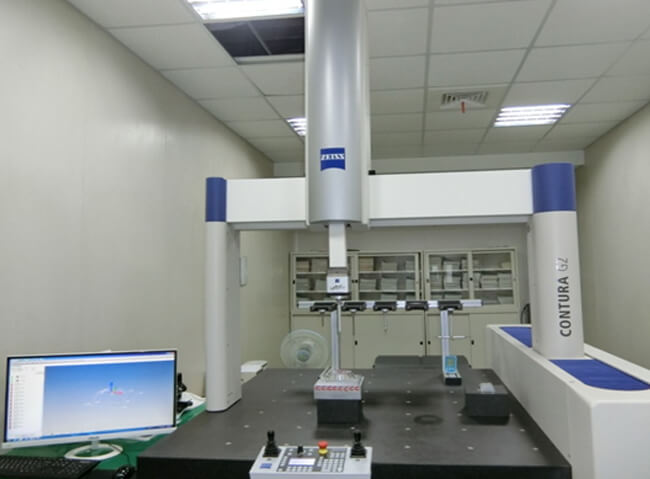
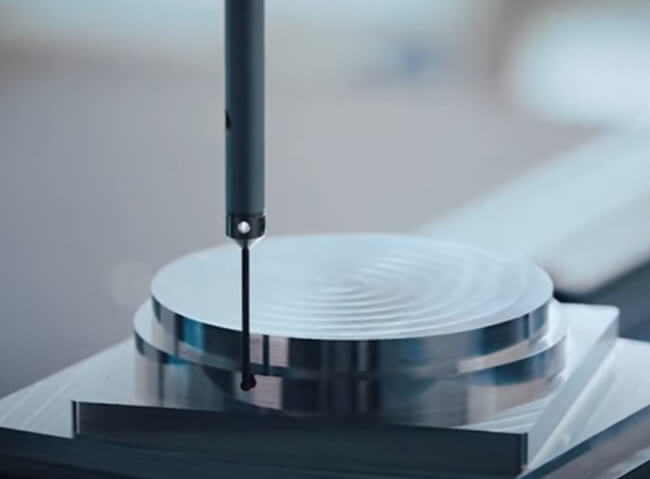
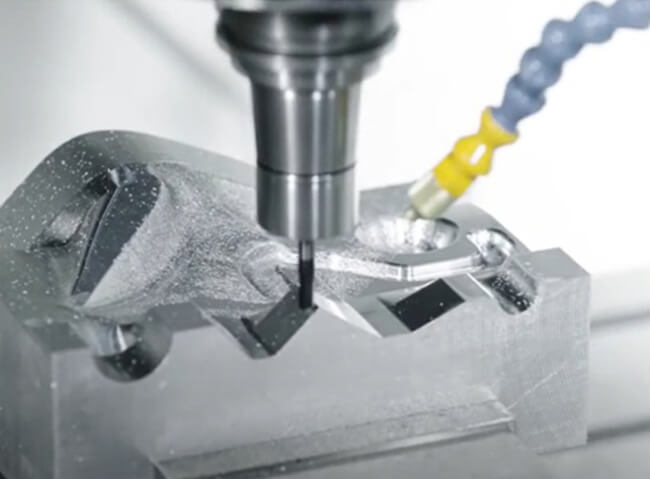
Each machine must be inspected by precision instruments and dynamic cutting tests that meet international standards.
The standard test piece that has been cut needs to be tested by a three-dimensional measurement to ensure that the accuracy meets the standard. (Comparison of the 3D file with the actual work-piece)
Specification:ISO 10791-7